USA
Problem Solving: Techniques. Part Three
This is the final and the most interesting for me part where I would like to talk about techniques of continuous improvement. This concept implies well-managed systems of control, management and motivation. It is impossible to improve without solving problems. The entity that does not develop becomes noncompetitive and vanishes. I hope that this article will give at least a slight push to your ideas of self-improvement.
1. Failure Mode & Effects Analysis (FMEA)
Studying all possible negative scenarios at the stage of planning is the main weapon in our arsenal. First, we solve the problem at a much lower cost than it could be at a later stage. Second, we grow professionally. What’s more, we understand the working processes much better. Let’s examine the scheme as an example of root cause.
Areas of application: moderately complex and complex problems
Process step: Just like before, the first step is to identify the problem.
Potential Failure Mode: Identify potential problems which could arise on the way.
Potential Failure Effects: What impact could potential problems make?
Severity: Estimate the «severity» of the problem according to a 10-point scale.
Potential Causes: Draw the root cause(s) for each failure (using RCA to identify them).
Occurrence: Estimate the occurrence according to a 10-point scale, where 10 is the most probable.
Current Controls: Existing measures to prevent the problem from occurring.
Detection: Estimate the level of detection with existing measures according to a 10-point scale, where 10 is the lowest. That is, 10 points will mean that existing measures are totally unable to deal with the problem.
RPN: Risk Priority Number, calculated by multiplying the three scores, Severity, Occurrence and Detection, RPN = Severity x Occurrence x Detection.
Action Recommended: Points to decrease Occurrence level or increase Detection level.
Responsible: who is responsible for the implementation.
Actions Taken
Actions Taken do not complete the process yet. Each action goes through the same estimation stage for Risk Priority Number until the problem is considered resolved.
The main task is to break down the problem to the potential points of priority fault. (RPN). The fault with the highest RPN is the target. The whole process is divided into ten basic steps but works as a cycle:
2. Kaizen
Kaizen is more of philosophy than of a technique. It claims that any process can be perfected. It is based on the idea of continuous improvement; therefore, the number of ways to implement it is limitless. According to Kaizen, each employee is responsible for finding gaps in the system, and each employee, regardless of the position and level of involvement, offers ways of perfecting the system.
Kaizen is aimed at performance, efficiency and elimination of waste. Waste can be of several types:
- Movement – useless activities
- Time – time wasted without any use
- Defects – failures which lead to redoing work
- Over-processing – excessive work
- Variations – excessive options when the standard way is satisfactory
Form of waste | Examples |
---|---|
Movement |
|
Time |
|
Defects |
|
Over-processing |
|
Variations |
|
I suggest using Kaizen system in the following way:
- Keep a log of solutions or arrangements which seem to you inefficient or improvable. Naturally, it is better to write them down the moment they are detected than to try to remember the whole list at the end of a sprint as retrospective.
- Once a month (frequency may vary) spend some time on finding the areas where you have wastes (you may start with yourself, and then, when you are sure that the techniques is working, use it for your team). The entries in the log can be used as input, and the table Forms of Waste – as a checklist. Think how you could get rid of wastes.
- Plan when the changes are going to be introduced. Do not play all your cards at once – the benefit of changes must be traced and analyzed. Otherwise it will be impossible to understand what exactly had a beneficial result. Do not overlook how your changes affect other areas.
- If changes affect other members of your team, do not fail to consult them and inform about upcoming events. Their comments might help to see the situation from a different perspective.
I started by saying that Kaizen is a philosophy rather than a tool. That is why there are so many ways of its application. For example, you can align your personal growth with Kaizen:
Kaizen Self Audit Checklist
To summarize the above, I would like to emphasize that the purpose of this article is not to set rules, but to show the variety of options at the path of problem solving. Every mistake made carries all information necessary for that, you just need to learn how to distinguish it. I hope this text will give, even small, but momentum to your self-improvement ideas.
Category | № | Description | Check | |
yes | no | |||
Motivation | 1 | Can I motivate myself? | ||
2 | Can I set goals by myself and achieve them? | |||
3 | Do I manage my time well? | |||
4 | Do I often try to escape responsibility? | |||
Communication | 5 | Do I express my ideas and points of view clearly?; | ||
6 | Do I listen to other people’s opinion? | |||
7 | Is it easy for my colleagues to work with me? | |||
8 | Do my soft skills help me to solve issues easily? | |||
Growth | 9 | Do I allow time for my professional growth? | ||
10 | Does my current project allow me to grow? | |||
11 | Have there been positive changes in me as a specialist over the past month? | |||
12 | Do I have a plan for growth for the near future? | |||
Work process | 13 | Do I provide proper quality control on the project? | ||
14 | Do I keep within estimates? | |||
15 | Do I keep statistics / analyze my work? | |||
16 | Do I contribute new ideas / influence the project perfection? | |||
Areas to perfect: | Score (=total ‘yes’/16) |

Vlad has been engaged in software development since 2009. Over the years, he had a chance to get a deep understanding of the process and related problems. Today Vlad works a Test Engineer and is responsible for improving the software development process, preventing defects, and spotting errors in functioning of the product.
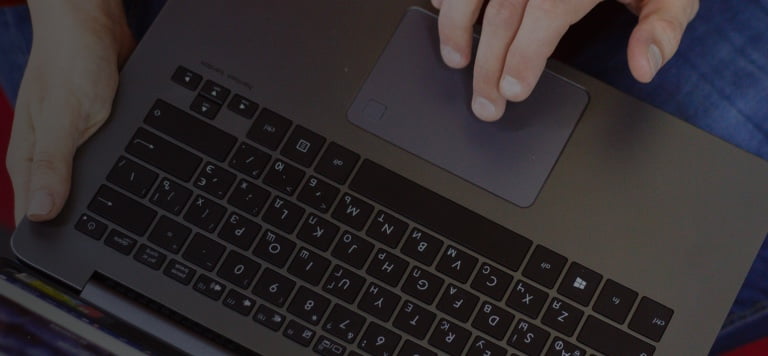
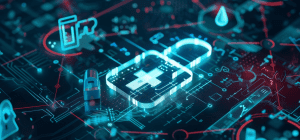
Explore how artificial intelligence is reshaping the battle against Fraud, Waste, and Abuse in health insurance. In this article, we’ll break down the key chal...
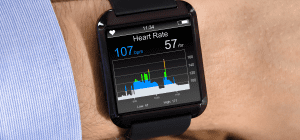
Chronic conditions such as heart failure, diabetes, and COPD require continuous oversight, but most healthcare systems still rely on periodic in-person visits. ...
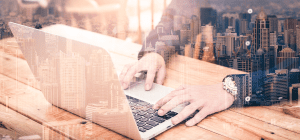
Innovation and digitalization drive growth in Central Asia, forming a new digital excellence hub with software development centers across several countries. Uzb...